It’s another day at the terminal: the vessel queue is growing, the ship’s crew is watching the clock, and all you can think is: how can we get this ship unloaded faster?
If you’ve ever asked yourself that question, you’re not alone. Bulk terminals around the world are under increasing pressure to handle higher volumes in less time. While many managers consider adding manpower or investing in larger equipment, one key factor is often overlooked: crane and grab cycle speed.
In this blog, we explore why it matters and how to improve it.
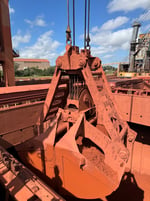
First things first, what do we mean by crane speed?
Crane speed isn’t just about how fast the crane lifts or lowers, it’s the total time to complete one full grab cycle: hoisting, slewing, positioning, grabbing, and releasing. In operations, this is often measured in cycles per hour and expressed in Free Digging Rate (tonnes per hour).
To give you an idea: a typical gantry ship unloader completes around 60 cycles per hour during the free digging phase.
Every second counts and costs
As an experienced terminal manager, you know how quickly small time losses can escalate. Every delay in your cycle reduces the number of grabs per hour, which slows down vessel turnaround. The result? Higher demurrage costs, pressure on berth planning, and delays throughout the logistics chain.
That’s why optimizing crane performance is key to keeping operations on schedule and on budget.
Let’s speed things up
Crane speed is no small detail. It directly impacts your terminal’s productivity and bottom line. While increasing the speed is not only about the crane, understanding the role of different crane types is essential, as they help define the setup and shape how your operation performs.
Gantry ship unloaders vs. mobile cranes:
- Gantry Ship Unloaders run on rails and move the grab in a straight path from A to B. This allows for faster, predictable cycles, ideal for standardized terminal setups like steel plants.
- Mobile cranes are more flexible and can use various attachments (grabs, spreaders, hooks). However, they tend to have slower cycles due to added slewing and luffing time. They’re often used in multi-purpose terminals or where space is limited.
With this in mind, here’s the reality: in most bulk terminals, you don’t get to pick your crane. The crane type, size, and positioning are usually dictated by the product you handle, the ships you serve, and the logistics around your terminal. But that doesn't mean you’re out of options.
If you can’t change the crane, change the game
The grab becomes your biggest lever for improving speed. Fine-tuning the crane–grab combination is one of the fastest ways to make a real impact on cycle speed and overall productivity, and it’s often an opportunity that’s overlooked.
Grab speed: the key to faster cycles
The grab’s opening and closing time directly impacts your cycle rate. Since lifting and lowering speeds are typically limited by the crane, upgrading to a faster and lighter grab can make all the difference.
An optimized grab design:
- Reduces cycle time with faster opening/closing
- Handles more payload due to lower self-weight
- Performs better not just during free digging, but also during trimming
Trimming is where most time is lost and where a fast, responsive grab makes the biggest difference. The right design helps reduce repositioning, improves cleanup efficiency, and speeds up final discharge.
Before we conclude, let us show you a combination that has led to significant efficiency improvements in recent years.
At VLI’s Pecém terminal, switching to optimized grabs resulted in a productivity boost of over 20%. First by upgrading to a faster Clamshell Grab, then further improving results with the NemaX Grab, thanks to quicker opening/closing, safer operation, and faster changeovers.
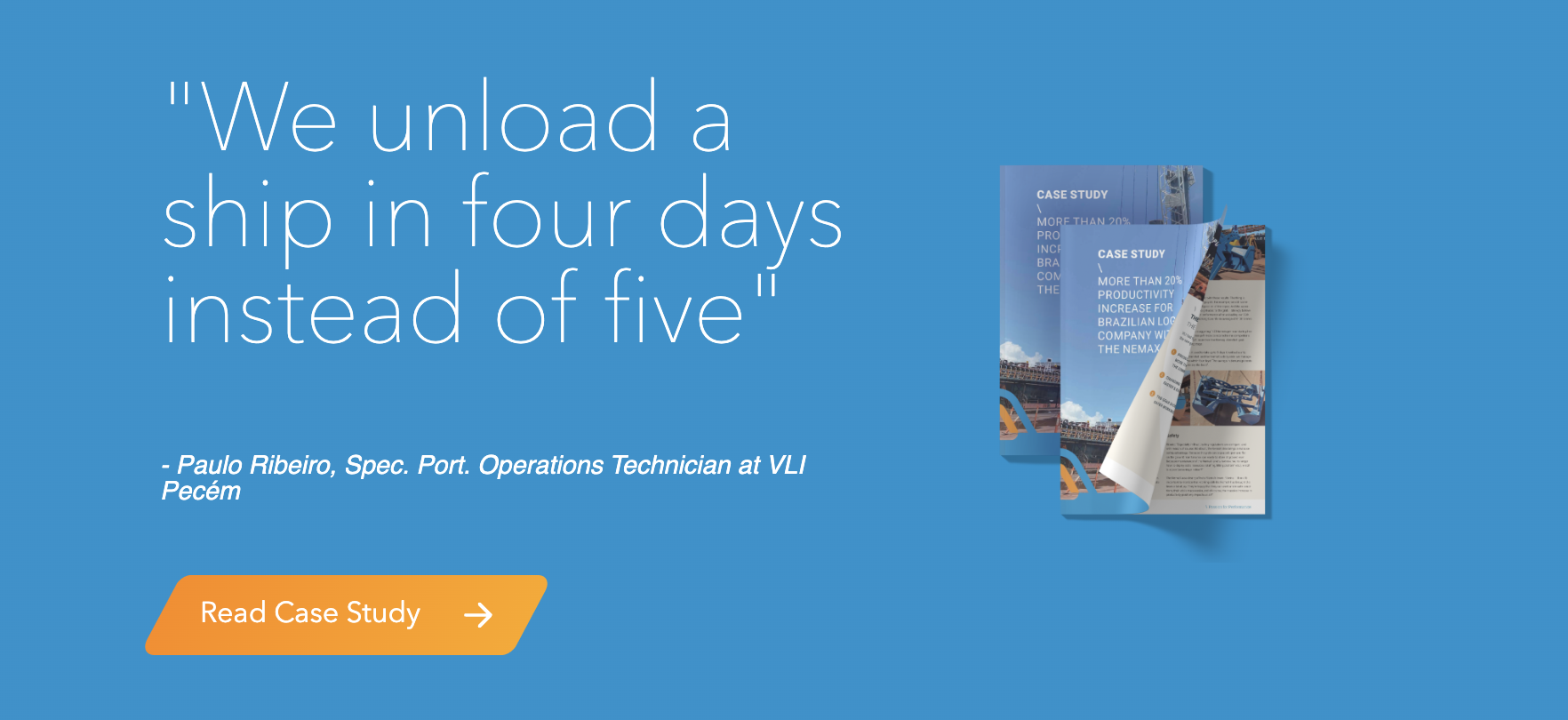
Improving terminal productivity isn’t always about investing in bigger cranes or adding more resources. As we’ve seen, optimizing cycle speed — especially by selecting the right crane-grab combination — can deliver significant results without major infrastructure changes. Small technical upgrades, like faster-opening grabs or lighter designs, can translate into real operational gains: faster unloading, lower demurrage costs, and better berth availability.
Are you curious how you can optimize your terminal setup without major investments?
Get in touch with our team, we’re happy to discuss how the right grab solution can help you boost your productivity. Feel free to contact us or book a meeting to find the best grab type for your application to boost your loading and unloading productivity.